Ensure optimal replenishment orders
with Freight Optimization
Holding an optimal level of inventory is key to maintain service levels and avoid stockouts while minimizing the costs associated. However, replenishment orders cannot always be emitted when needed. Some providers may establish certain constraints that the orders need to satisfy, like ordering a minimum quantity or fulfilling a unit of transportation with the products ordered, for example. Keeping up with all these requirements may become a burden in the replenishment and stock planning processes. To solve that, the Freight Optimization tool is included in ForgeFlow's Demand Driven solution.
Freight Agreements
Freight Agreements collect all the different constraints requested by a specific provider. The constraints that can be specified in a freight agreement are multiple, including:
- Minimum order price
- Minimum and maximum weight of the order
- Filling a unit of transportation
- Global Minimum Order Quantities (MOQ), among others
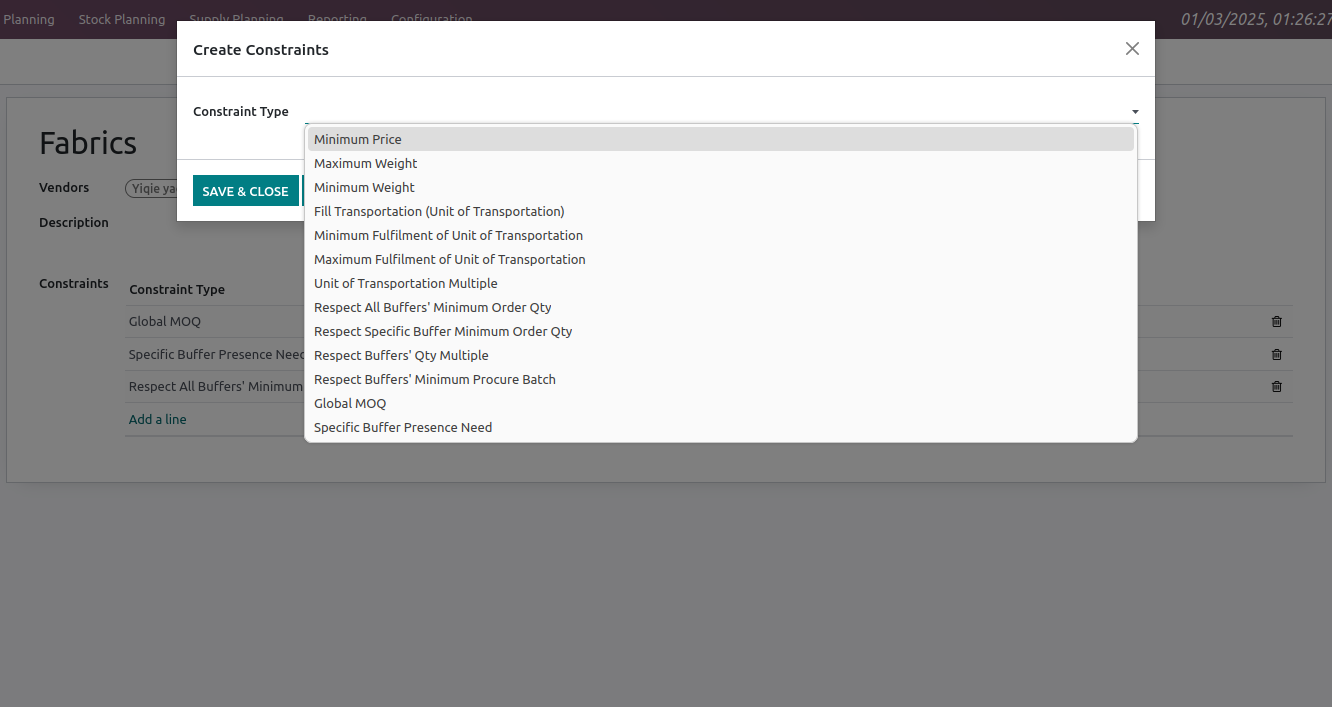
Procurement alerts
When a product from a supplier involved in a freight agreement is to be procured, the system alerts the user, indicating the involvement in a freight agreement and providing the option to start a new freight optimization process. This ensures that freight agreements and their constraints will always be considered.
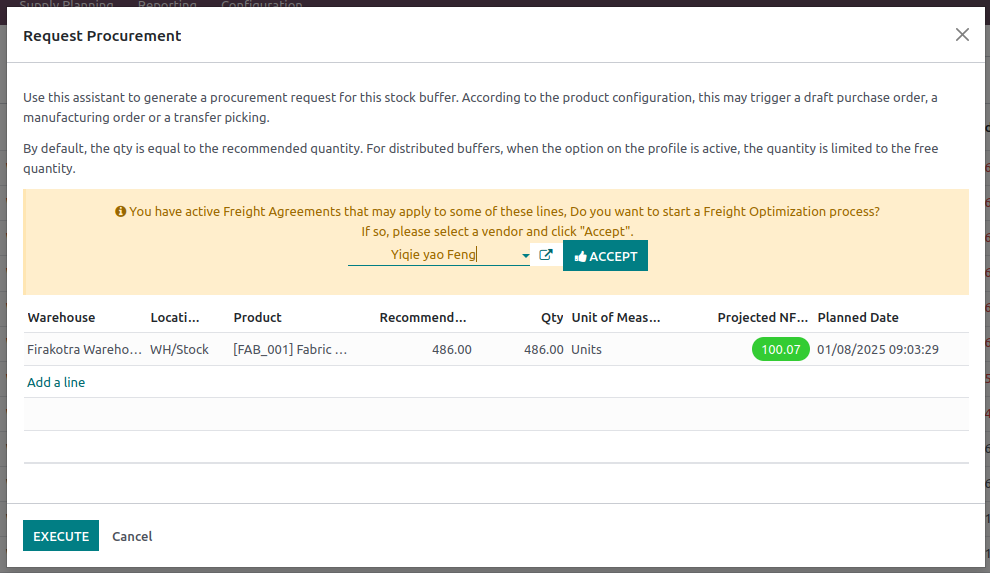
Freight Optimization process
To compute a freight optimization, users need to select the corresponding vendor and the products that are to be replenished in the order. If a constraint requires to order a specific product when one of the selected ones is ordered, the system will show a message alerting of the situation, and no further action will be allowed until that product is included in the order too.
Upon confirming the required products and starting the freight optimization process, users can compute the recommended order quantities to fulfill the constraints.
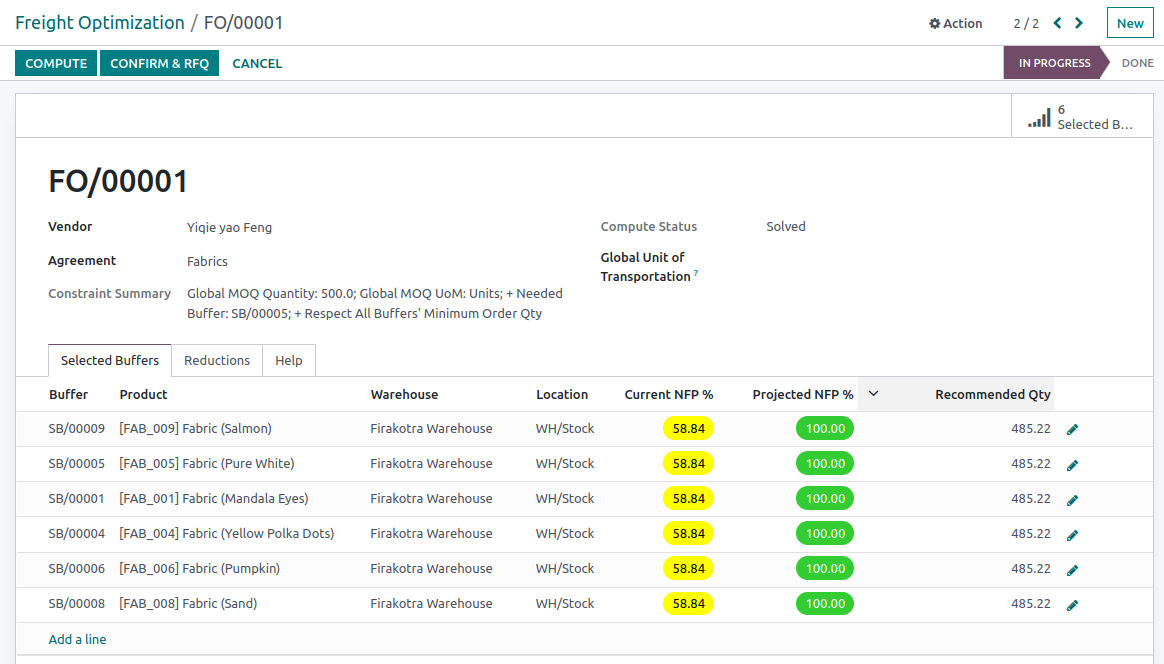
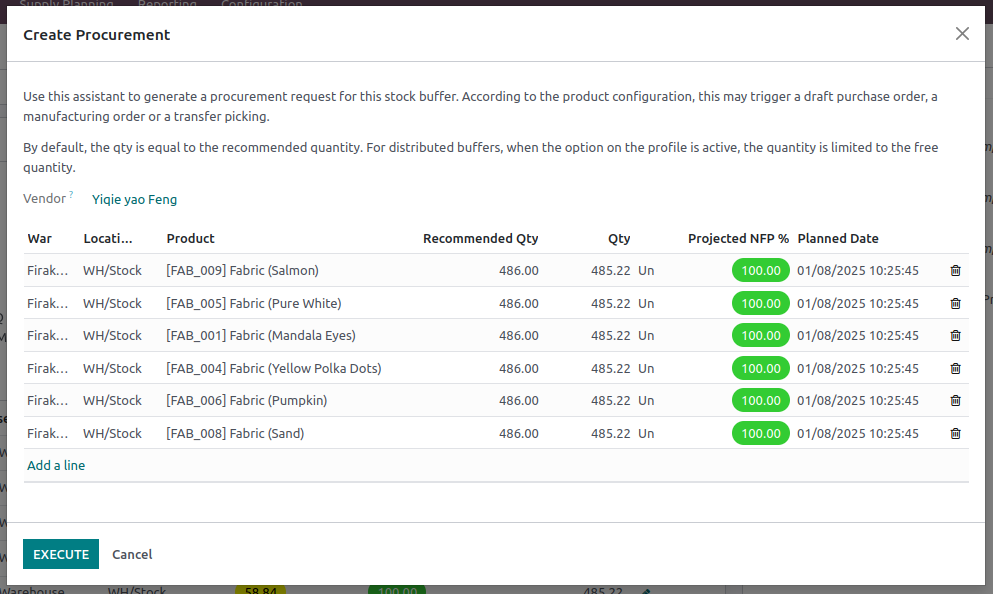
Generate Requests For Quotations
Initially, the freight optimization process may result in an overstock situation, especially when few products are selected. To minimize overstock, additional products with lower projected on-hand quantities should be added and the optimization recomputed.
Once satisfied with the optimization results, users can confirm the results and generate a Request for Quotation (RFQ) for all products involved.
Watch the tool in action
Explore our related articles
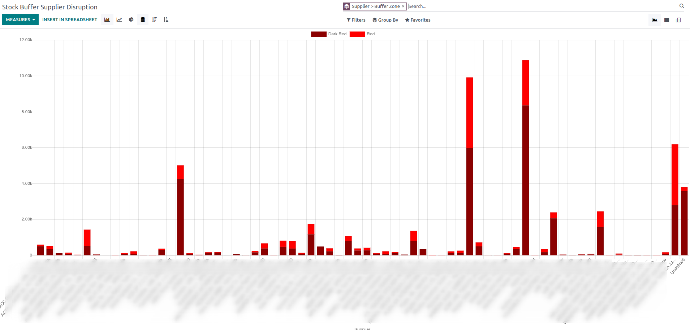
Improve supply reliability with the Supplier Disruption Report
This report evaluates supplier reliability by analyzing the time stock levels spend in critical buffer zones. Learn to identify unreliable suppliers and take corrective actions to maintain a steady flow of materials.
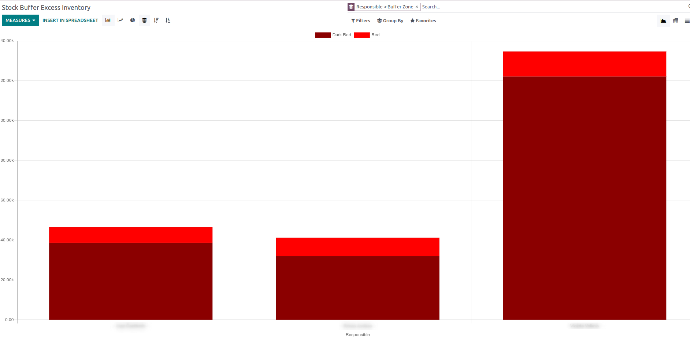
Evaluate stock managers reliability with the Excess Inventory Report
Use this report to evaluate the effectiveness in stock excess control. It analyzes the cost of excess inventory held, enabling comparisons with past periods to understand the evolution of the performance. This allows for a comprehensive understanding of inventory management efficiency.
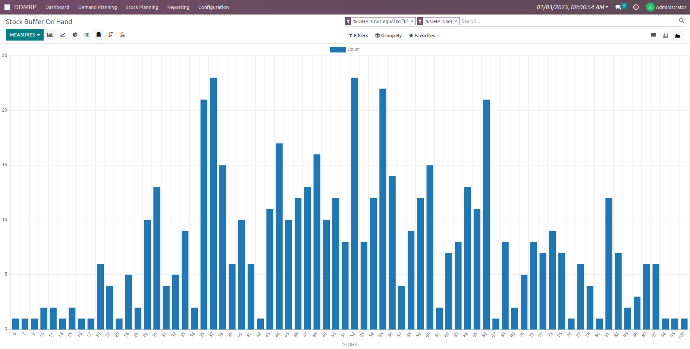
Assess inventory levels with the On-hand Distribution Report
This report shows the state of the inventories when compared to their respective optimal stock limit. This helps evaluate for which specific parts the company tends to hold too much stock and the overall inventory behavior of the company.