What is Demand Driven MRP?
Demand Driven MRP is able to deliver impressive results across a broad range of industries, with a growing number of major software providers now developing solutions aligned with DDMRP specifications.
This inventory planning tool leverages proven flow-based principles to enhance planning and execution in unpredictable environments where customer tolerance times are much shorter than the total lead times—a common challenge today.
Let's get started!
What does Demand Driven mean?
Demand Driven refers to the ability to "sense changing customer demand and adapt planning and production while pulling from suppliers all in real time".
What does it imply?
Demand Driven Material Requirements Planning is a formal multi-echelon planning and execution method to protect and promote the flow of relevant information and materials. The methodological foundation of DDMRP includes concepts from:
MRP
DRP
LEAN
TOC
Six Sigma
Innovation
What DDMRP is and is not?
DDMRP is...
Centered in actual demand and flow-based methods
Having an strategic amount of stock to cover demand
Optimizing inventory and reducing costs
"Position, protect, pull, and adapt"
DDMRP is not...
Centered in supply- and cost-based operational methods
Making to order everything
Putting inventory everywhere
"Push and promote"
Using DDMRP will improve all of the following aspects of your business

Service
DDMRP ensures a strong informational and material flow, which produces consistent and reliable results in meeting customer expectations.
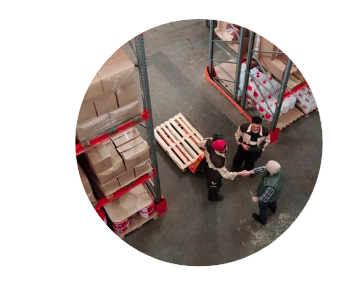
Inventories
A solid tool like DDMRP guarantees less time for products to move through the system and, therefore, a lower total inventory investment.
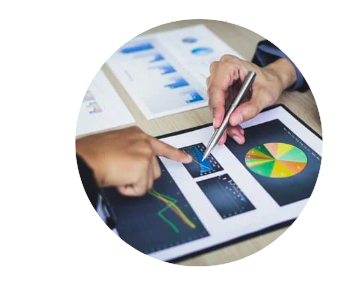
Revenue
When service is consistently high, market share tends to grow, and with it, the total revenue.
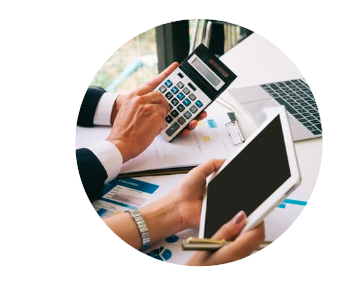
Expenses
Most of the activities that cause inefficiency and extra expenses such as overtime, rework, cross-shipping and expedited freight are minimized.
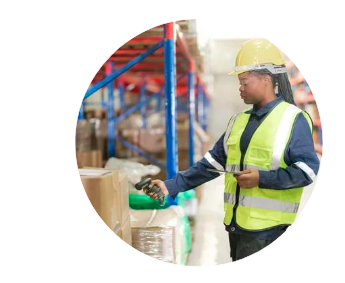
Quality
With DDMRP, fewer mistakes caused by confusion and expediting are made.
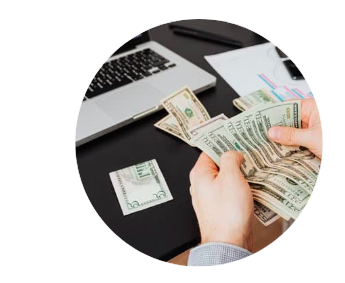
Cash
A good flow translates to materials being converted to cash at a relatively quick and consistent rate.
How?
DDMRP is essentially an enhancement to traditional MRP, following a cyclical pattern with six key components. Similar to standard MRP, DDMRP relies on specific configuration decisions and inputs to function effectively. While many inputs overlap with MRP, there are crucial distinctions that make DDMRP particularly effective in today's VUCA (volatile, uncertain, complex and ambiguous) environment.
A brief explanation of the six components of DDMRP:
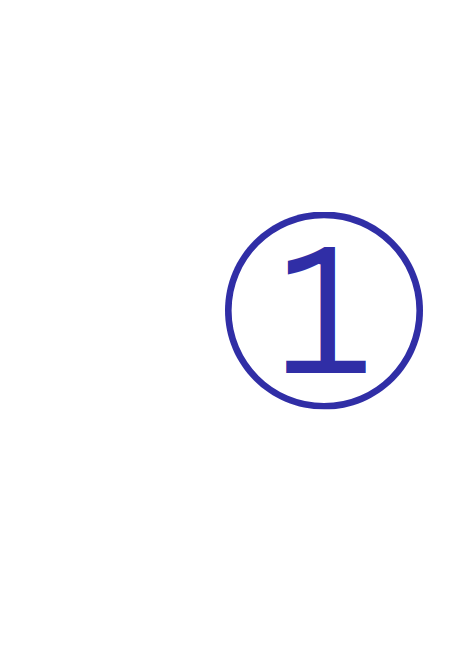
Strategic Decoupling
DDMRP begins with identifying strategic decoupling points, which act as supply chain safeguards against demand signal distortion and interruptions in supply, affecting both order creation and fulfillment. Deciding where to place these points is a strategic choice, as it impacts both customer lead times and inventory investments. DDMRP uses six specific criteria to determine optimal decoupling locations.

Buffer Profiles and Levels
To keep each point effectively decoupled, buffers must be appropriately sized. Each decoupled item in DDMRP is assigned to a buffer profile, which applies a set of settings to items with similar characteristics, such as lead time, tier within the product structure, and sensitivity to supply or demand fluctuations. Buffer profiles streamline the management of multiple decoupled items across an organization.
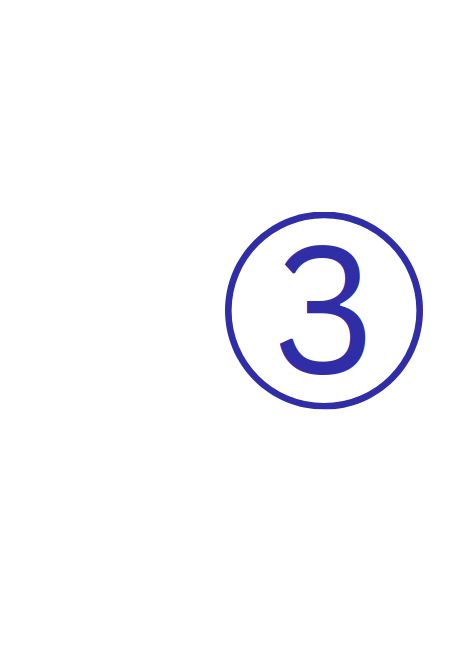
Dynamic Buffer Adjustments
In a rapidly changing, volatile environment, DDMRP adjusts buffers at decoupling points based on factors like demand rate, lead times, and profile changes, along with known events such as promotions or seasonal spikes. Many DDMRP-compliant systems automate these adjustments.
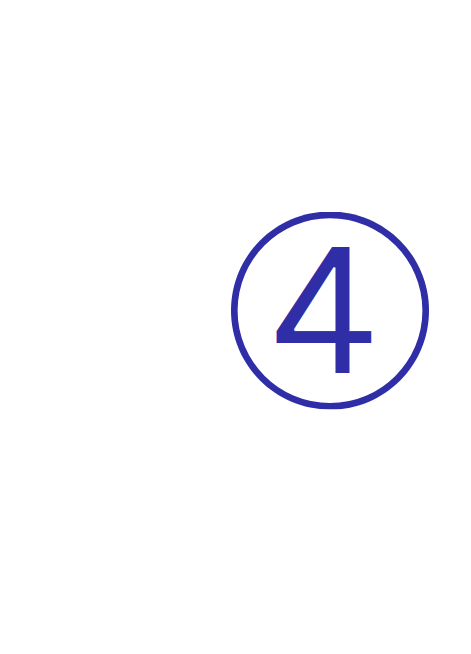
Demand Driven Planning
Demand-driven planning involves using specific supply order generation rules in the DDMRP model. These rules, collectively called the net flow equation, are applied daily across buffered positions. Dependent demand created at these positions moves down through subsequent levels in a process known as "decoupled explosion"
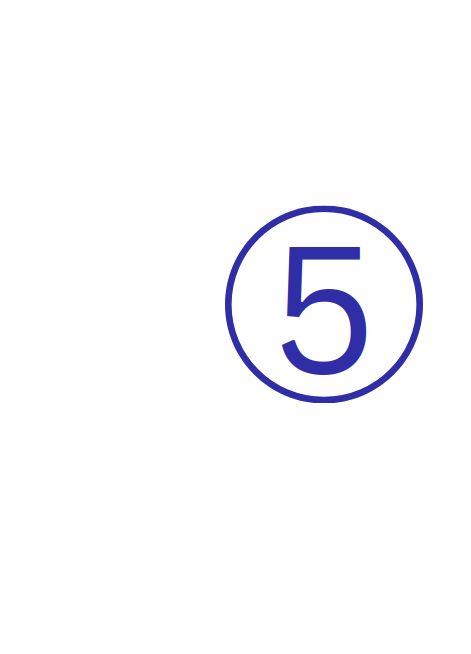
Visible and Collaborative Execution
In DDMRP, planning and execution are clearly separated. Planning ends once an order recommendation is approved and becomes a scheduled receipt. Execution then manages open orders through two types of alerts -Buffer Status Alerts and Synchronization Alerts- aimed at addressing potential flow disruptions that could affect customer commitments or buffer stability.
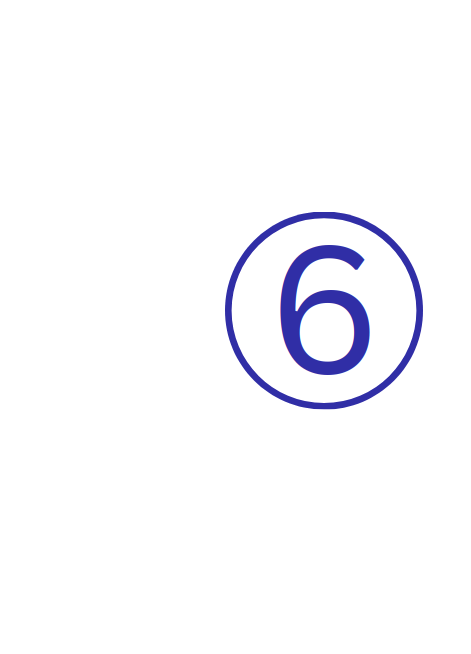
Tactical Adaption
The final DDMRP component oversees adjustments to the DDMRP model, which relies on the foundational settings defined by the first three components. This adjustment cycle, known as Demand Driven Sales and Operations Planning (DDS&OP), incorporates past performance and future forecasts. Unlike traditional models, DDS&OP eliminates the need for a master production schedule (MPS) and introduces essential updates to standard practices, supporting a dynamic DDMRP implementation.
Simply put, DDMRP offers a clear, step-by-step methodology that is:
Transparent
Intuitive
Easy to interpret
Consistent
Sustainable
DDMRP Results
DDMRP has achieved remarkable results across diverse industries. Below are highlighted typical outcomes when DDMRP is implemented effectively, supported by proper training and compliant software.
On time fill rate performance
Lead time reductions in
several industry segments
Inventory reductions while
improving customer service
Costs related to expedite activity and false signals are largely eliminated
Planners see priorities instead of constantly
fighting the conflicting messages of MRP
We are officially certified
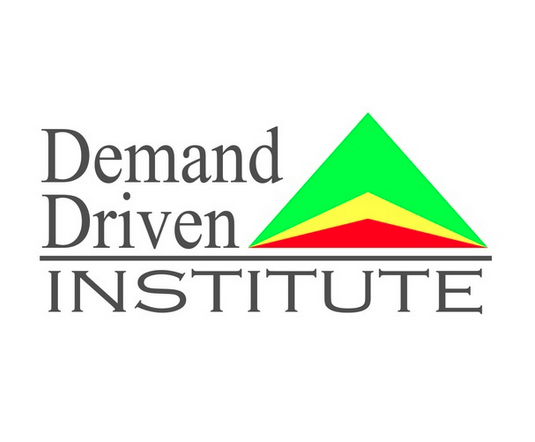
At ForgeFlow, we recognize the substantial benefits of Demand Driven Material Requirements Planning (DDMRP). This is why we implement it for our customers, adhering closely to established compliance standards approved by the Demand Driven Institute.
DDMRP Compliant
DDS&OP Compliant
DDOM Compliant